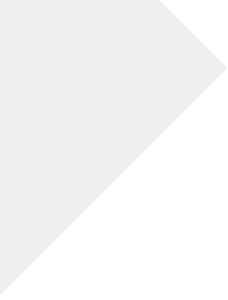
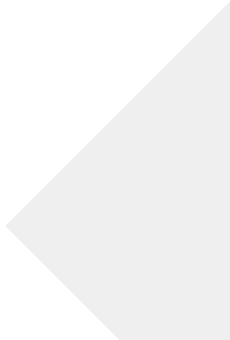
栄光化学では、最新鋭、高性能の成形機を充実させ、射出成形技能検定1級取得者6名を筆頭とし、社外のスクールや講習を通して社員一人ひとりの知識レベル、技術レベル等の向上を図っています。
最新鋭の設備と豊富な経験、知識により汎用樹脂からLCPやPPSといった超高機能性樹脂まで対応出来る生産技術を備えており、作業効率、品質、安全性、環境配慮といった側面から改善提案を行い、Challenge to be Betterの精神を目指しています。
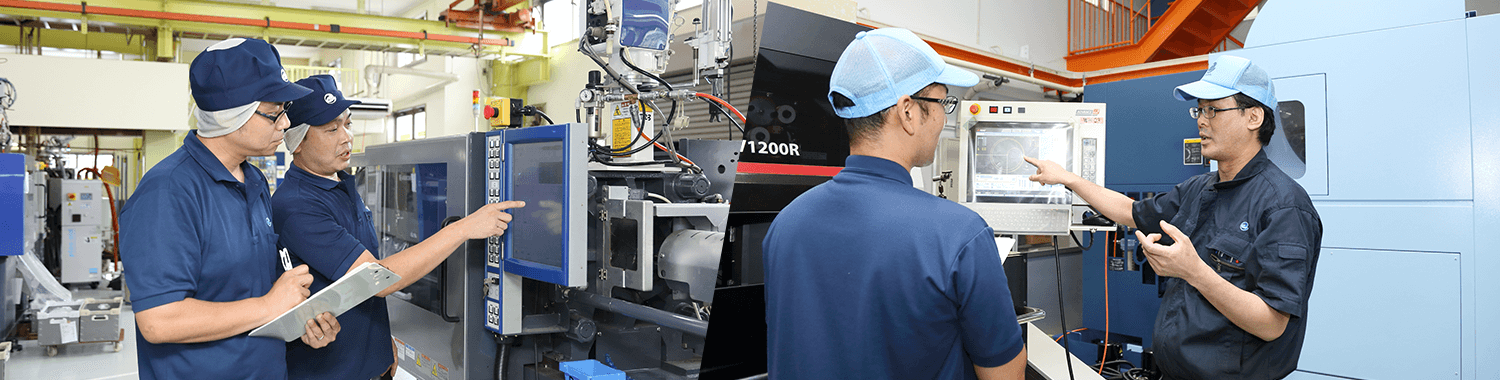
肉薄部の無人量産化に成功
問題点
極薄の肉厚製品で金型を分割する必要が有ったため、薄肉部の製品が破断してしまう不良が発生。
その為1回/日は金型をメンテナンスする必要があり成形者の業務負荷が高かった。
改善事例結果
極薄肉厚は比較的小さな抵抗でも破断してしまう為、普段は気にしないレベルの引張り抵抗でも製品が破断してしまう。
金型サイズを大きくしない様にスライド無での型構造を模索し、量産無人化に成功。
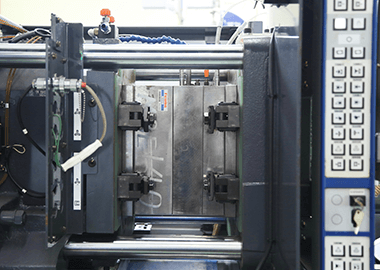
オリジナルのサブマリンゲート形状
問題点
サブマリンゲートというゲートの自動切断機構では切断時のゲートカスによりPL面(パーティング面)にゲートカスが残り、金型を傷めたり、製品にゲートカスを挟んだ事によるバリ不良が発生する。
改善事例結果
なぜゲートカスは発生するのかという原理を物理的に模索し、樹脂の種類毎(靱性や強度など)で当社オリジナルのサブマリンゲートの機構を模索しゲートカス低減に成功
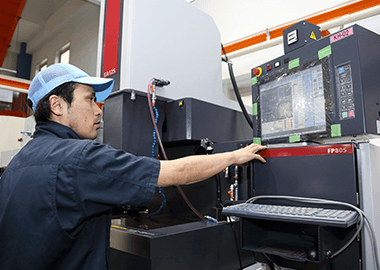
離型剤散布の半自動成形の全自動化
問題点
定期的に離型剤を散布しないと離型時に製品形状が変形する為、離型剤散布の半自動成形を行っていたが成形負荷が高かった。
また半自動成形の為、夜間中に稼働できず生産効率が悪かった。
改善事例結果
製品形状として可動側での離型抵抗が大きく型割変更も困難なため、離型時の押し上げ機構を特殊タイプに変更し、離型剤の散布無しで量産無人化および24時間稼働に成功。
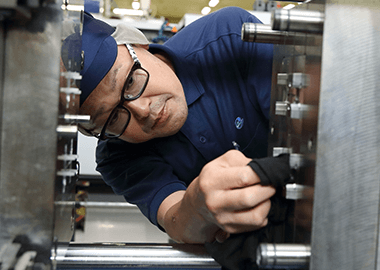
PID制御による型温の安定化
問題点
100℃以上の高温金型の製品(透明品)を量産していると、時折製品に気泡不良が発生していた。
改善事例結果
温調機だとON/OFF制御による水温の温度バラツきがあるため、温調機構をPID制御の棒ヒーターに変更し金型温度を安定化する事で気泡不良を撲滅に成功。
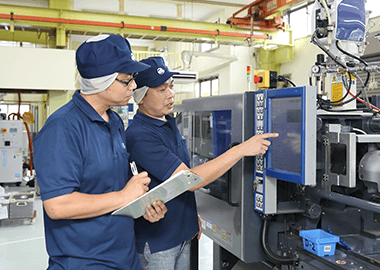
ファジィな位置決めによるインサートカメラ検査
問題点
成形品の超音波圧入インサートが複数ある製品だが、1箇所づつインサートを実施する必要があるため作業者が作業漏れをしてしまう事があった。作業漏れの流出防止で員数管理や再検査等を実施していたが、管理負荷が高くなっていた。
改善事例結果
位置決めを必要としないコンベア上に流せばよいカメラ検査を製作し、インサート5箇所有無を判定出来るようにした。
位置決め治具等を必要としない事で検査機投入の負荷もかからず、さらに員数管理などの管理負荷を省く事に成功。
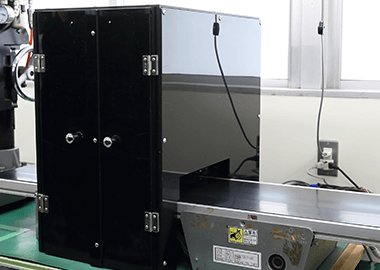
超小物製品の検査自動化
問題点
成形品が超小物の為に人間の目視検査難易度が高く、不良品流出防止の為に同一ロットの2度目検査、3度目検査を実施しており検査負荷が高かった。
改善事例結果
超小物の製品の為、そのメリットを生かし検査機の設置スペースをとらない様に小型の自動カメラ検査機を導入。
従来の検査時間が150h/月以上かかっていたが、カメラ検査の導入により検査員の検査負荷を大幅低減に成功。
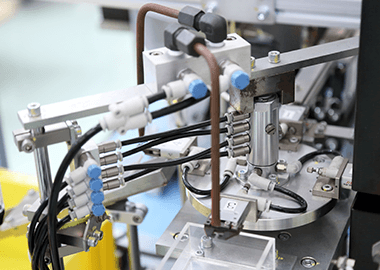
鋼材選定による金型破損の撲滅
問題点
樹脂圧力により一部の入子に荷重がかかってしまい入子破損が定期的に発生しており、破損した入子の金型修理や品質管理の両面で大きな負荷がかかっていた。
改善事例結果
樹脂圧力が一部箇所にかかってしまう事象は避けられない為、入子部分のみ鋼材の種類を再検討。
複数の鋼材を模索・検証する中で、選定された鋼材により入子破損の撲滅に成功。
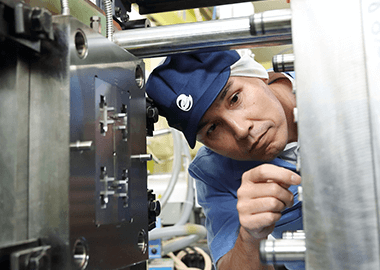